Selecting the right screw pin type shackle can be a game changer for industries reliant on securely linking equipment or rigging. These shackles are a staple in various sectors, highly regarded for their resilience and versatility. Delving into their utility and design will unveil why they are deemed indispensable.
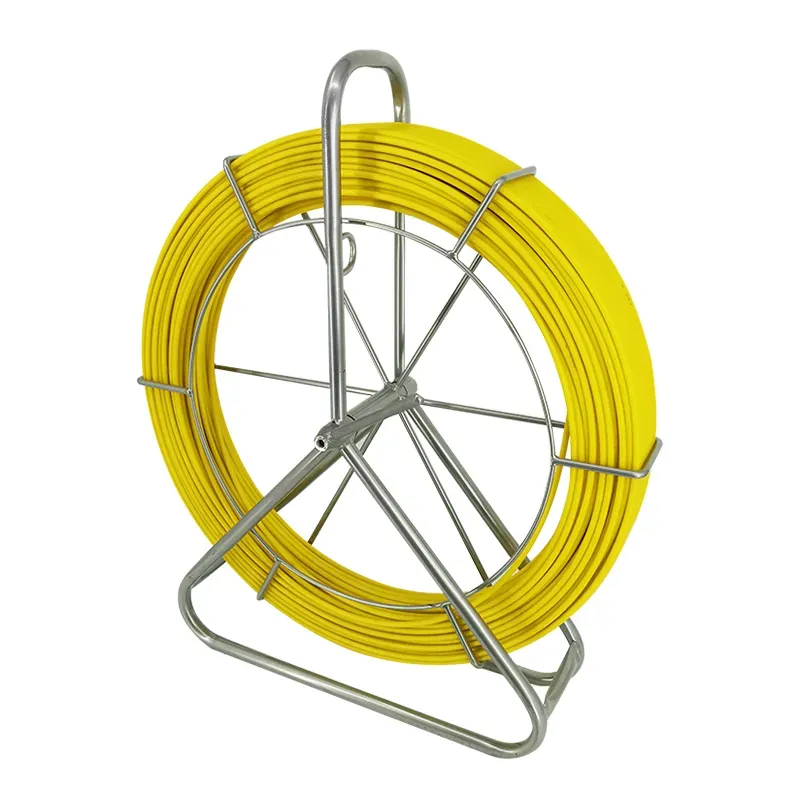
Screw pin type shackles, crafted from robust materials like stainless or galvanized steel, are engineered to withstand formidable loads. These shackles feature a unique screw pin design, which simplifies the connection process while providing a high level of security. When you work in environments demanding durability and safety, such as construction, maritime, or even outdoor adventure gear, the efficiency and reliability of screw pin shackles become apparent.
Expertise in the field underscores the importance of selecting the appropriate size and load rating. Shackles are cataloged with Working Load Limits (WLL), ensuring that they can accommodate specified weights safely. Industry professionals emphasize that choosing a shackle with a suitable WLL is not merely a recommendation but a necessity for preventing workplace accidents. Thus, understanding the load requirements and specifications is crucial.

The expert use of screw pin type shackles involves stringent adherence to safety protocols. Before usage, inspecting the shackle for any visible signs of wear or deformation is critical. One must ensure that the threads on the screw pin are intact and not compromised by corrosion or damage. This pre-use assessment is vital in maintaining operational safety.
Authoritative voices in safety and engineering advocate for a regular maintenance schedule, especially in demanding environments. Routine lubrication can mitigate the risk of metal-on-metal wear that can lead to thread damage. Additionally, keeping the shackles free from exposure to harsh chemicals or severe environmental conditions prolongs their service life.
Trustworthiness in using screw pin type shackles is further developed through brand reliability and manufacturer certifications. Reputable manufacturers subject their products to rigorous testing and quality assurance processes to meet international safety standards like those set by OSHA or ANSI. Validating the manufacturer's compliance with these standards instills confidence in the product's integrity.
screw pin type shackle
User experience also plays a fundamental role. Those who have utilized screw pin type shackles over time often share testimonials about their ease of use compared to bolt type shackles. The quick-release feature of the screw pin allows for rapid attachment and removal, enhancing productivity without compromising on security.
Furthermore, adaptable for various applications, screw pin shackles can be easily incorporated into unique settings or setups. Whether it’s securing equipment in rugged outdoor environments or stabilizing heavy loads in a controlled environment, their versatility continues to meet the unique demands of different industries.
Innovation in shackle technology is also noteworthy. Advancements such as the incorporation of corrosion-resistant coatings and the utilization of innovative materials maintain the shackles' functionality even in adverse conditions. Such continuous improvements stem from a deep understanding of industry needs and a commitment to enhancing product performance.
For industries where the cost of failure is high, investing in reliable screw pin shackles is non-negotiable. Selecting the right shackle is a matter of balancing cost with safety and performance, and it’s a decision best guided by both engineering knowledge and practical experience. As the industry progresses, innovations in design and material composition are likely to further enhance these indispensable tools' reliability and safety.
The strategic deployment of screw pin type shackles, rooted in deep industry knowledge and authoritative manufacturing practices, assures businesses of securing operations with a tool that is as strong in reputation as it is in functionality. By adhering to best practices in selection, maintenance, and application, entities can ensure optimal operational safety and efficiency.